As a professional manufacturer of supercritical CO2 extraction machines, BIT understands that every customer has unique needs. Choosing the right extraction system requires considering production scale, material characteristics, delivery time, and operating costs.
This Supercritical CO2 Extraction Equipment Selection Guide shares key factors. It helps you decide the most suitable extraction solution.
[Read More] Supercritical CO2
Define Your Production Schedule
Your production timeline plays a crucial role when purchasing supercritical CO₂ extraction equipment. Are you planning to start production in the next quarter? In three months? Or do you need to begin immediately? Your timeline will directly impact equipment selection and delivery arrangements.
Custom Manufacturing & Delivery Time
Most equipment requires custom manufacturing based on your specific requirements, including:
- Extractor vessel size
- Pressure range
- Automation level
- Separation system configuration
Production and testing may take 1 to 6 months, depending on equipment complexity and factory schedule.
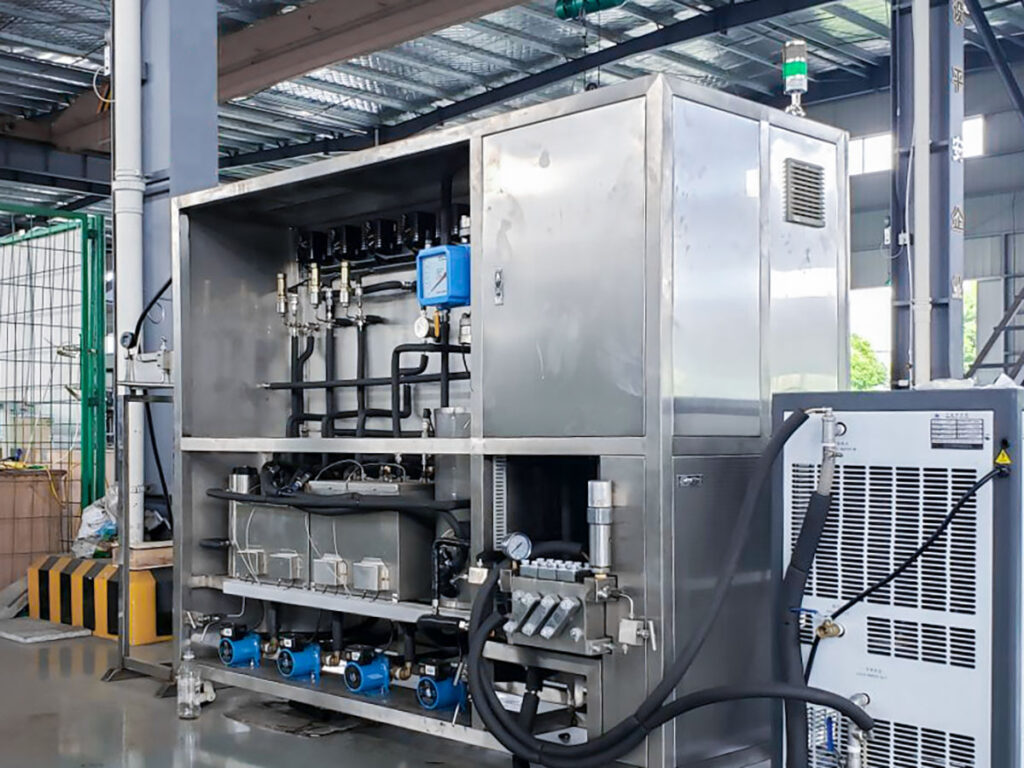
Our Recommendations
- We discuss the delivery timeline in detail before purchase to ensure no delays.
- Our team provides efficient installation & commissioning for faster production startup.
- We offer short-term solutions such as small-scale trial equipment or leasing options if you have an urgent project.
2. Determine Your Processing Capacity
To select the right extractor, first define your daily processing capacity. We provide different equipment categories to meet various production needs:
Equipment Type | Application | Processing Capacity (Dry Material) | Vessel Volume | Typical Use Case |
Lab-Scale | R&D, Formulation Testing | 50g-5kg/batch | 0.5L-5L | Research, Product Development |
Pilot-Scale | Small-Scale Production | 5kg-50kg/batch | 5L-50L | Essential Oils, Plant Extracts |
Industrial-Scale | Large-Scale Manufacturing | 50kg-2000kg/batch | 100L-5000L | High-Volume Continuous Production |
Example – Rose Essential Oil Extraction
If your target is to process 500kg of dried rose petals per day and each batch takes 2 hours, suitable equipment options include:
- 100L-500L single extractor vessel operating in rotation
- Dual or triple extractor systems for higher efficiency
- Fully automated CO₂ extraction system for stable, high-efficiency production
Our Recommendations
- We recommend the optimal equipment size based on your daily production needs.
- If you plan to expand production, we provide modular systems for easy scaling.
3. Consider Material Characteristics & Moisture Content
Material properties significantly affect extraction efficiency, especially moisture content and particle size.
How Moisture Content Affects Extraction
- Supercritical CO₂ extraction works best with materials containing ≤10% moisture.
- If moisture is too high, pre-drying (e.g., vacuum or low-temperature drying) is required.
- High moisture reduces efficiency and increases energy consumption.
Particle Size & Packing Density
- Proper grinding increases CO₂ contact surface, enhancing extraction.
Our Recommendations
- We optimize pre-processing to maximize extraction efficiency.
- Our engineers assist in adjusting pressure, temperature, and flow rate for the highest extraction yield.
4. Automation & Ease of Operation
Different automation levels impact efficiency and labor costs. Choose based on your production needs:
Automation Level | Features | Best for |
Manual Control | Operator adjusts parameters | Lab research |
Semi-Automatic | Partial automation, some manual intervention | Pilot production |
Fully Automatic | Pressure, temperature, CO₂ recovery, and flow control are automated | Industrial production |
Optional Monitoring System
Real-time production monitoring for enhanced safety and traceability.
Our Recommendations
- Small-scale production? Choose semi-automatic for cost savings.
- Large-scale production? Go for fully automated systems for efficiency and stability.
- We offer monitoring & data management systems to keep track of operations.
5. Operating Costs & CO₂ Recovery System
Besides equipment price, operating costs must be considered:
Key Cost Factors
- CO₂ consumption – High-efficiency CO₂ recovery reduces gas loss.
- Energy consumption – Pumps, heaters, and cooling systems affect electricity costs.
- Maintenance costs – Includes seal replacements, pump servicing, and pipeline cleaning.
Our Recommendations
- Our systems feature high-efficiency CO₂ recovery, minimizing gas loss.
- Energy-efficient design optimizes heating and cooling, cutting power costs.
- We provide comprehensive maintenance support for long-term equipment stability.
Conclusion
As a supercritical CO₂ extraction equipment manufacturer, we are committed to providing high-efficiency, customized solutions. When selecting your system, consider:
✅ Production timeline – Ensure timely equipment delivery.
✅ Daily processing capacity – Choose the right scale for your operation.
✅ Material characteristics – Optimize pre-treatment for efficiency.
✅ Automation level – Balance efficiency and cost-effectiveness.
✅ Operating costs – Reduce CO₂ and energy consumption.
Best Equipment for Rose Essential Oil Extraction
For rose oil production, we recommend 100L-1000L industrial-scale extractors with:
- CO₂ recovery system for cost efficiency
- Fully automated control for smooth operation
Why Choose Us?
- Customized solutions – Tailored to your production needs
- Fast delivery – Clear production schedule to meet deadlines
- Energy-efficient design – Lower costs, higher profitability
- Comprehensive after-sales support – Installation, training, and maintenance
Why Choose Us?
- Customized solutions – Tailored to your production needs
- Fast delivery – Clear production schedule to meet deadlines
- Energy-efficient design – Lower costs, higher profitability
- Comprehensive after-sales support – Installation, training, and maintenance
Looking for the best supercritical CO₂ extraction system? Contact us today for expert advice and customized solutions!