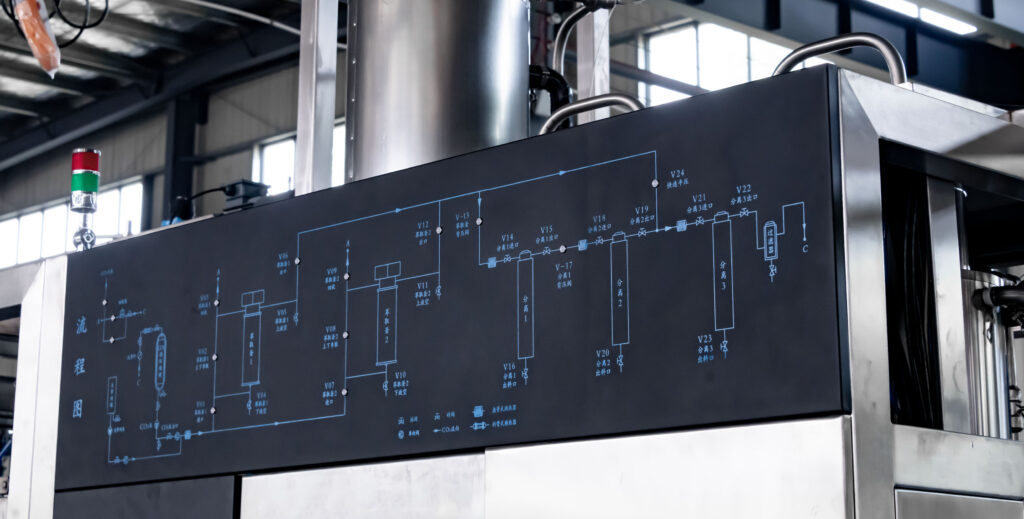
Over 30 years of design and production of supercritical CO₂ extraction Machine
Supercritical CO2 Extraction Process
Essential Oil Extraction Equipment | GMP Certified Industrial Extraction Solutions
Supercritical CO2 extraction technology has revolutionized the extraction of natural compounds, offering an efficient and environmentally friendly alternative to traditional methods. By utilizing carbon dioxide in its supercritical state, this technique enables the precise separation of desired components without leaving harmful solvent residues. This guide delves into the principles, equipment, process, and applications of supercritical CO2 extraction, providing a complete overview for industry professionals and enthusiasts alike.
Why Has Supercritical CO2 Extraction Become an Industry Standard?
Redefining Efficient Extraction through Scientific Principles
Supercritical CO2 extraction leverages CO2’s unique properties when it surpasses its critical temperature (31.1°C) and pressure (73.8 bar). In this state, CO2 exhibits both gas-like diffusivity and liquid-like solvating power, making it an exceptional solvent for extracting a wide range of compounds. By fine-tuning temperature and pressure, operators can selectively dissolve specific components, enhancing extraction efficiency and product purity.
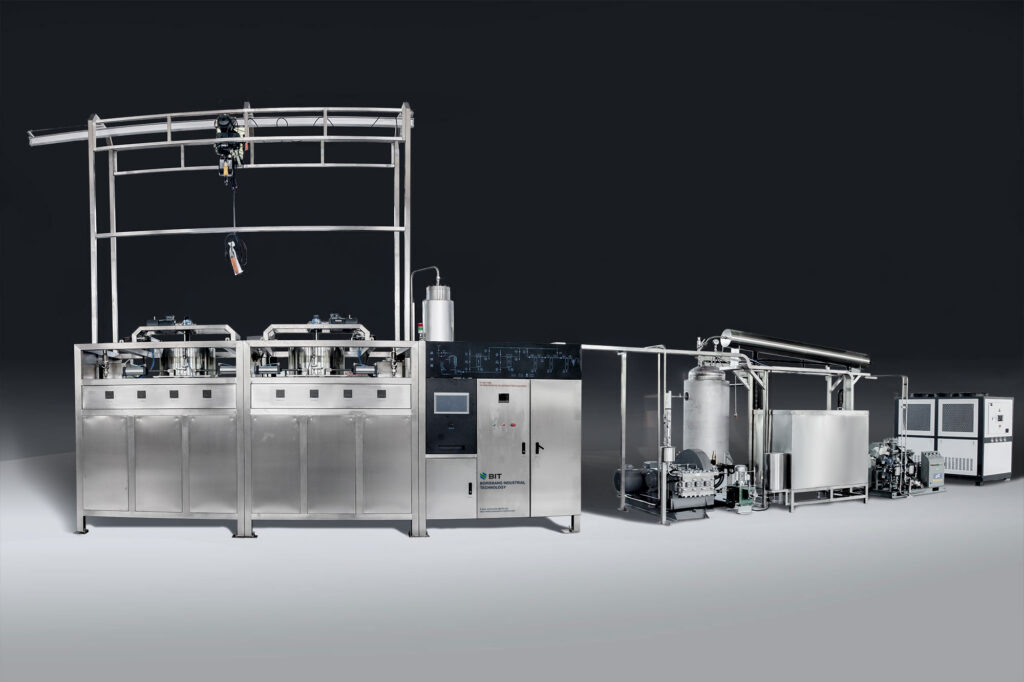
Diverse Applications Across Multiple Industries
The versatility of supercritical CO2 extraction has led to its adoption in various sectors:
- Essential Oils: Extracting high-purity oils from plants like lavender, rose, and jasmine.
- Food Industry: Decaffeinating coffee and tea, extracting flavors, and isolating antioxidants.
- Cosmetics: Obtaining natural ingredients for skincare and beauty products.
- Pharmaceuticals: Isolating active compounds from medicinal herbs for drug formulation.
In-Depth Analysis of Supercritical CO2 Extraction Equipment
Core Components and Technical Specifications
A typical supercritical CO2 extraction system comprises several key modules:
- CO2 Supply System: Maintains a steady flow of CO2, ensuring consistent pressure and temperature conditions.
- High-Pressure Pump: Elevates CO2 to supercritical pressure levels, typically up to 500 bar, with flow rate precision of ±0.1 L/min.
- Extraction Vessel: Constructed from 316L or 304L stainless steel, this chamber withstands pressures up to 1000 bar and accommodates varying batch sizes from 50L to 5000L.
- Temperature Control System: Utilizes electromagnetic induction heating to maintain temperature stability within ±0.3°C.
- Separation Unit: Employs a multi-stage pressure reduction (e.g., 50→20→5 bar) to precipitate extracted compounds, often monitored by online UV detectors for real-time analysis.
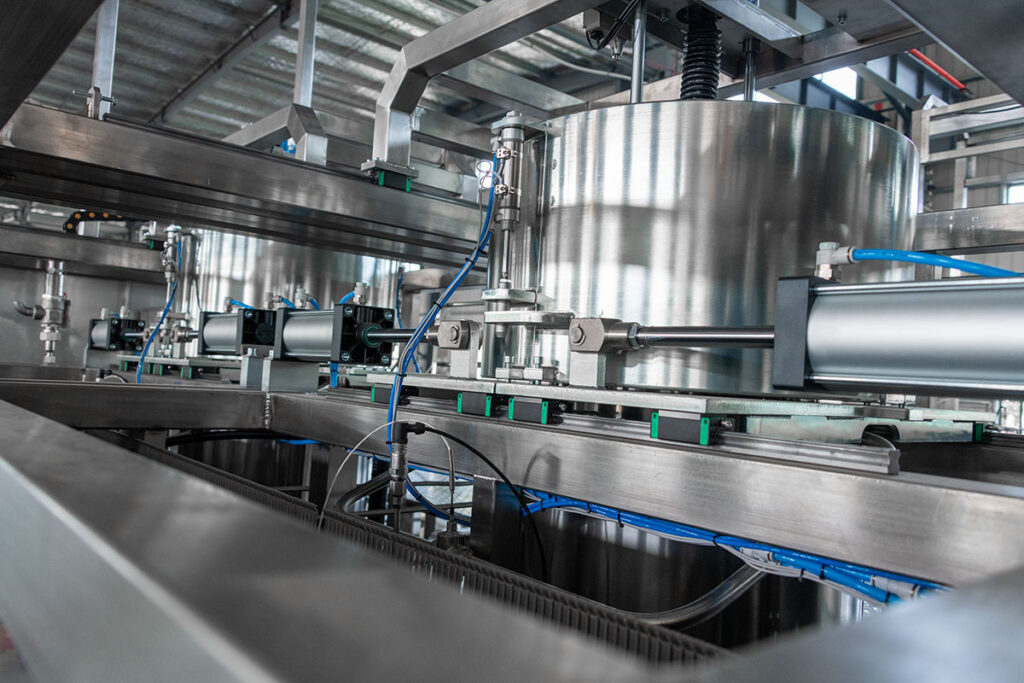
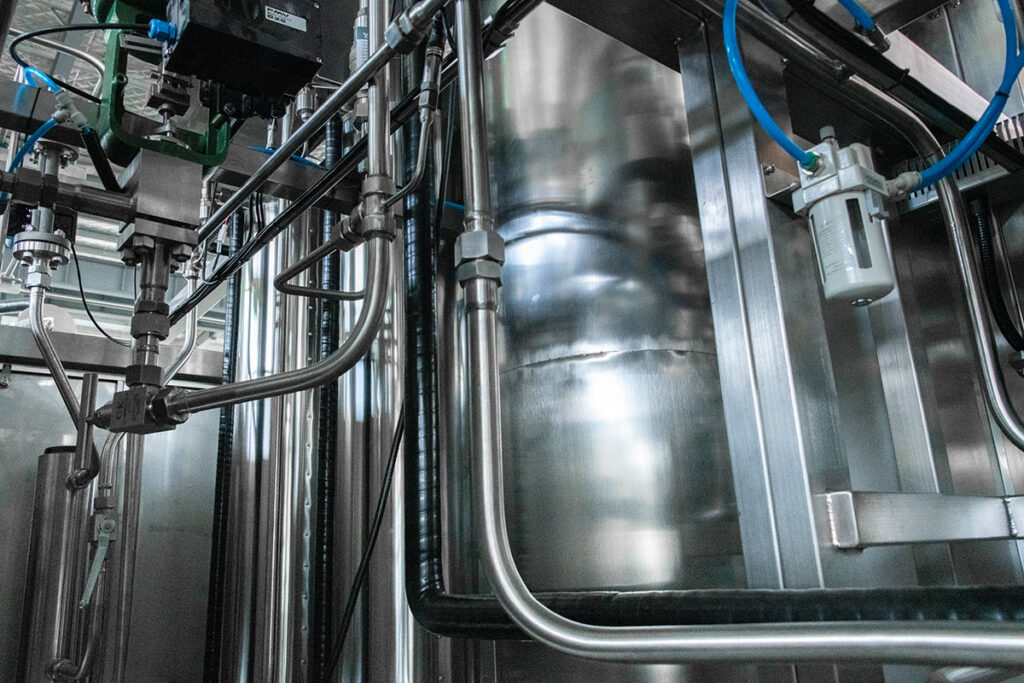
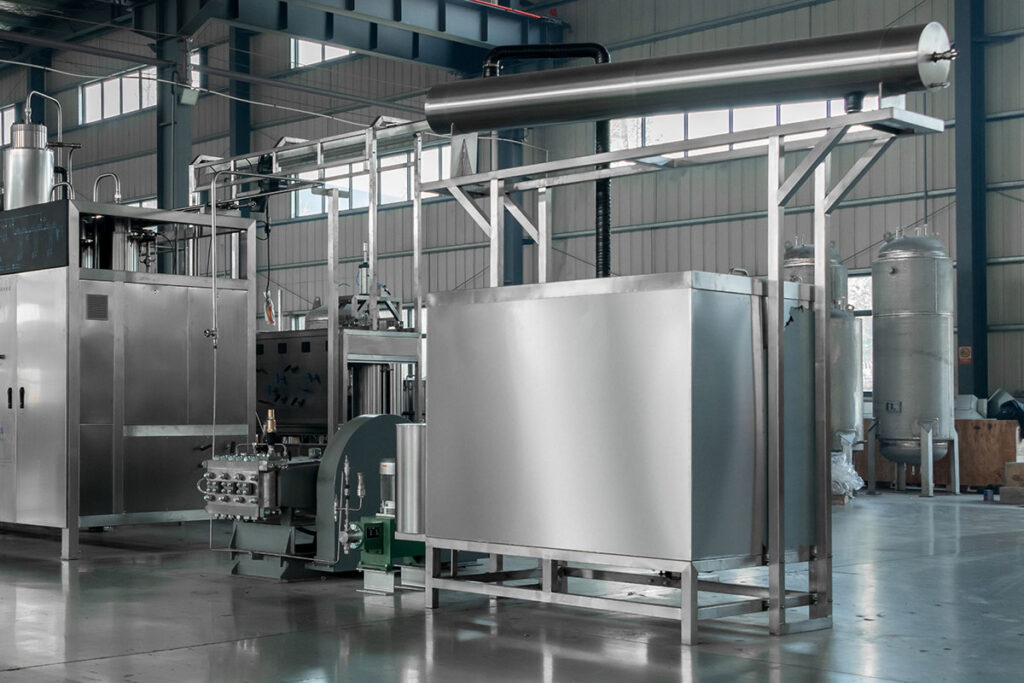
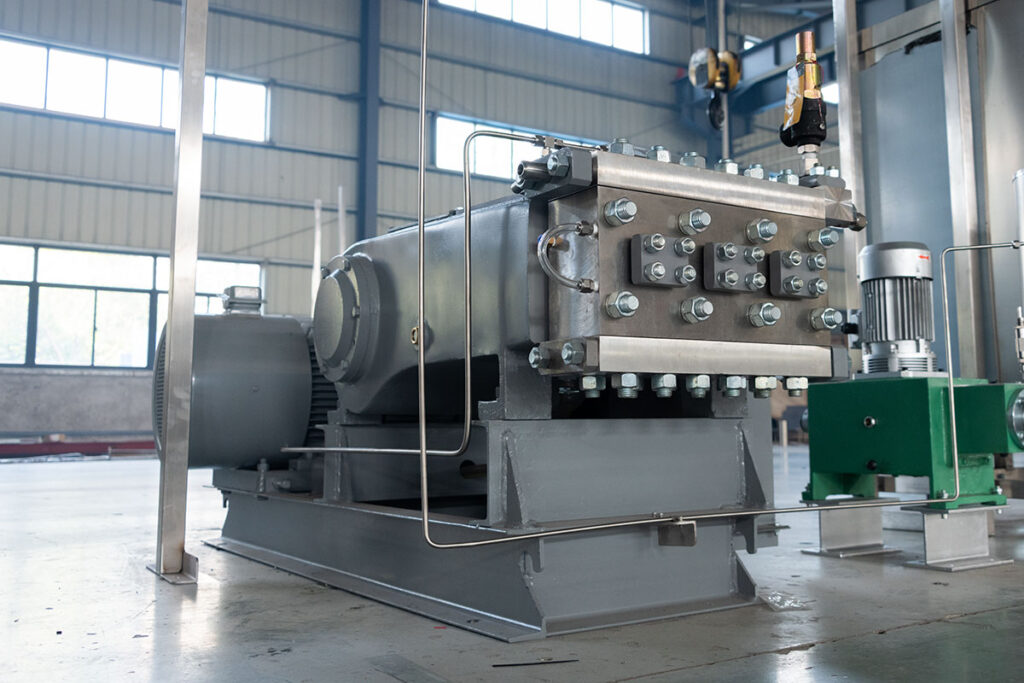
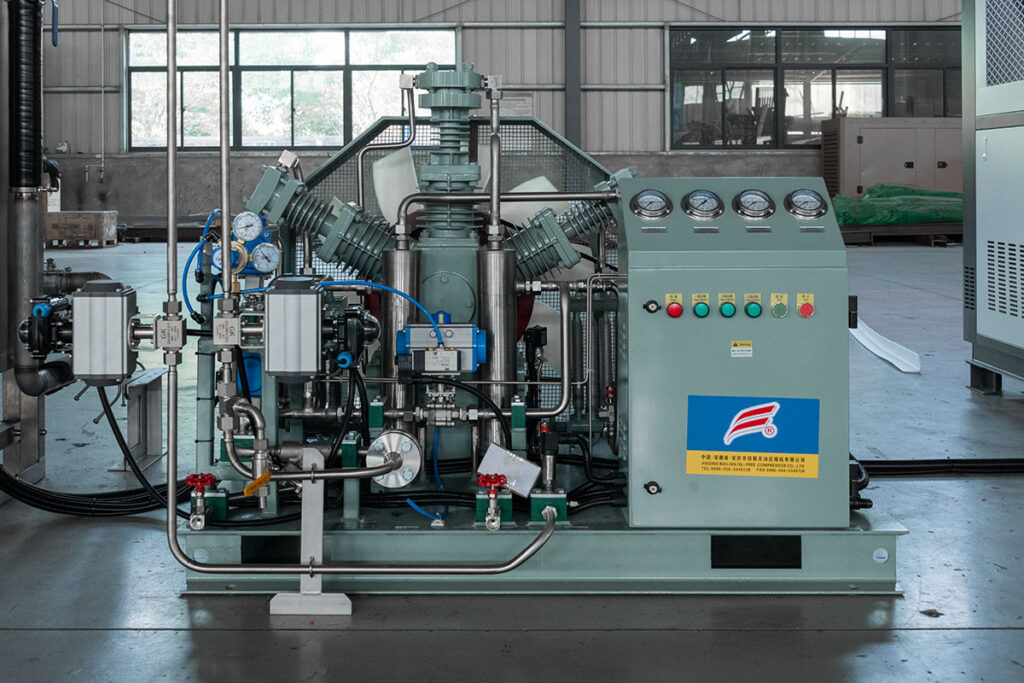
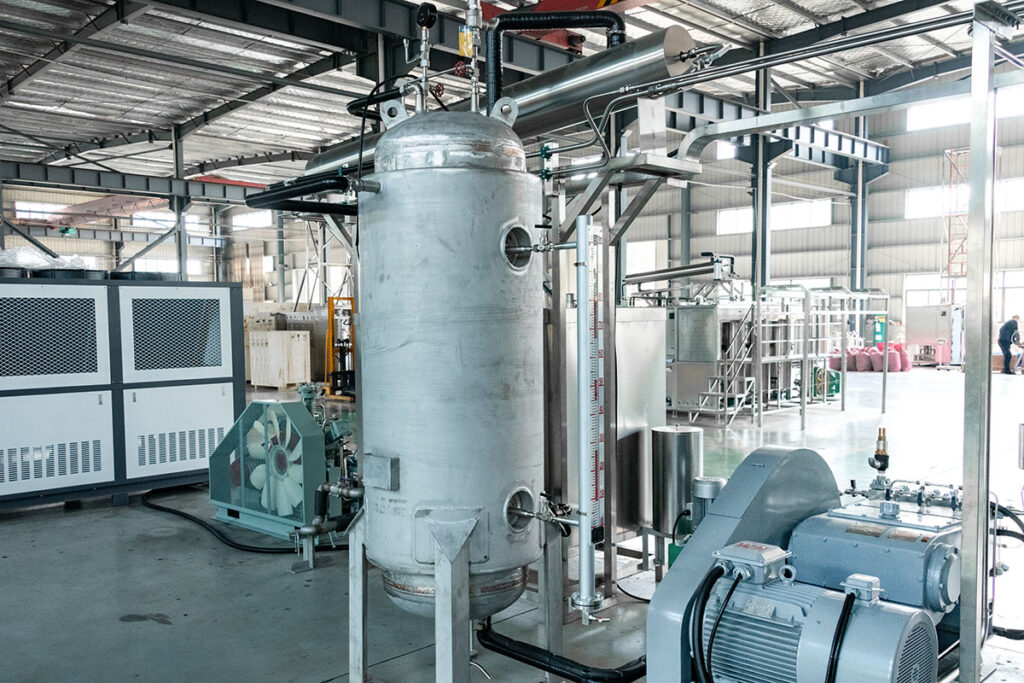
Five Critical Factors When Selecting Equipment
When choosing supercritical CO2 extraction equipment, consider the following parameters:
- Pressure Stability: Fluctuations should remain below ±0.5% to ensure consistent extraction selectivity.
- Temperature Precision: Maintaining control within ±1°C is crucial for preserving heat-sensitive compounds.
- CO2 Recovery Rate: Efficient systems achieve recovery rates above 98%, reducing operational costs.
- Automation Level: Advanced systems feature PLC and HMI controls to minimize human error.
- Energy Consumption: Aim for systems consuming less than 3 kWh/kg of product, aligning with EU CE certification standards.
How to confirm the model of supercritical CO2 extraction equipment that best suits your specific needs before purchasing? You can contact us for a free consultation and quote, or [click here].
Step-by-Step Overview of the Supercritical CO2 Extraction Process
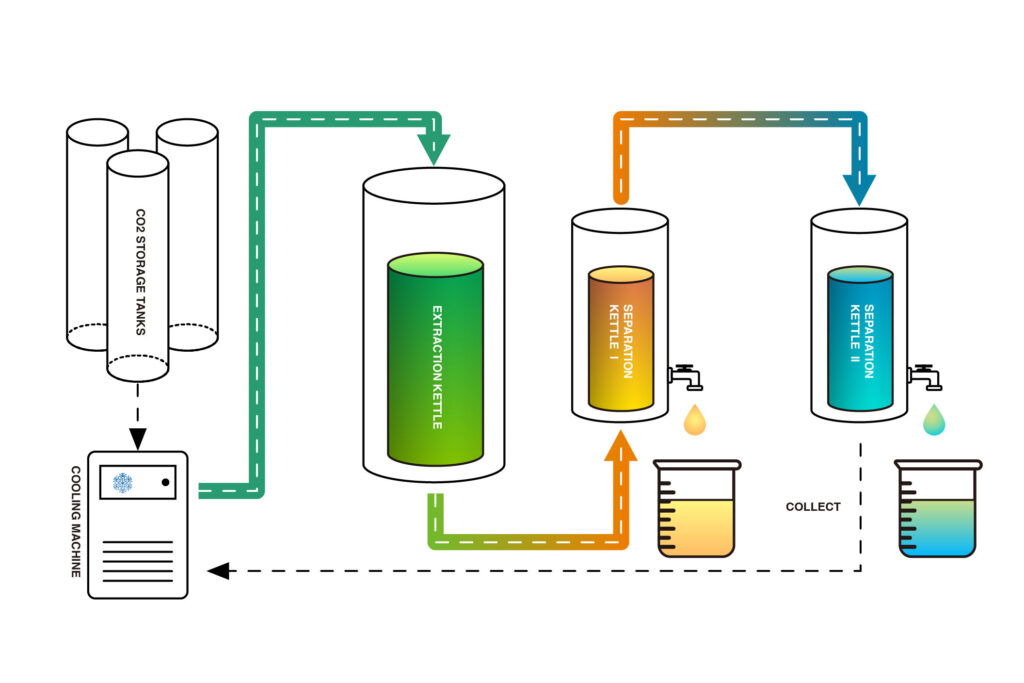
- CO2 Compression: CO2 gas is drawn from storage and compressed to reach supercritical conditions, enhancing its solvating capabilities.
- Introduction into Extraction Vessel: The supercritical CO2 is directed into the extraction chamber containing the raw material, facilitating the dissolution of target compounds.
- Solubilization and Separation: The CO2-solute mixture moves to a separator where pressure and temperature adjustments cause the solutes to precipitate out.
- CO2 Recovery and Recycling: The now gaseous CO2 is captured, cooled, and recompressed for reuse in the system, promoting sustainability.
- Product Collection and Storage: Extracted compounds are collected in designated containers and stored under conditions that prevent degradation, such as low temperatures or inert atmospheres.
Practical Guide to Industrial-Scale Production
Essential Pre-Processing Techniques
- Particle Size Reduction: Grinding plant materials to 40-80 mesh for herbs and 20-40 mesh for seeds enhances extraction efficiency.
- Moisture Content Adjustment: Drying materials to a moisture content of 8-12% prevents water-related extraction issues.
- Co-Solvent Addition: Incorporating 5-10% ethanol can improve the solubility of polar compounds.
Optimizing Extraction Parameters
Extraction efficiency can be modeled by the equation:
Extraction Efficiency = (Pressure × Temperature) / (Flow Rate × Time)
For instance:
• Essential Oil Extraction: Operating at 40°C and 250 bar with a flow rate of 0.8 m³/h·kg yields optimal results.
• Alkaloid Extraction: Utilizing 55°C and 350 bar with a 10% methanol modifier enhances alkaloid recovery.
Troubleshooting Common Issues
Issue | Potential Cause | Recommended Solution |
---|---|---|
Sudden Drop in Yield | CO2 Purity Below 99.9% | Switch to Food-Grade CO2 Source |
Separator Blockage | Improper Pressure Gradient | Adjust Multi-Stage Pressure Reduction Settings |
Excessive Energy Use | Heat Exchanger Fouling | Perform Monthly Cleaning with Citric Acid |
How to Optimize Supercritical CO2 Extraction Parameters: A Practical Guide [Read More]
Emerging Trends and Future Developments
The field of supercritical CO2 extraction is evolving rapidly, with innovations such as:
- Continuous Extraction Systems: Enhancing throughput by up to 300%.
- AI-Driven Parameter Optimization: Utilizing machine learning to fine-tune extraction conditions in real-time.
- Nano-Encapsulation Technologies: Integrating extraction and microencapsulation processes.
- Solar-Powered Operations: Reducing energy costs by up to 60%.
- Blockchain-Based Traceability: Implementing secure, transparent tracking of product origins and processing.
- Miniaturized Equipment: Developing desktop-sized units for research and small-scale production.
- Carbon Capture Integration: Creating closed-loop systems that utilize captured CO2, promoting negative carbon emissions.⸻
Conclusion
Supercritical CO2 extraction stands at the forefront of modern extraction technologies, offering unparalleled efficiency, selectivity, and environmental benefits. Its application across various industries underscores its versatility and effectiveness. As technological advancements continue to emerge, supercritical CO2 extraction is poised to play an increasingly vital role in sustainable production processes. 
Frequently Asked Questions (FAQ)
Q1: What is the cost range for supercritical CO2 extraction equipment?
Prices vary based on capacity and features. Laboratory-scale units (10L) range from $50,000 to $100,000, while industrial-scale systems (500L and above) can cost between $300,000 and $800,000.
Q2: How does supercritical CO2 extraction compare to traditional solvent methods in terms of cost savings?
This method can reduce overall costs by 30-50%, thanks to solvent recyclability, lower energy consumption, and decreased waste management expenses.
Q3: Is specialized training required to operate supercritical CO2 extraction equipment?
Modern systems are highly automated, featuring user-friendly interfaces and remote monitoring capabilities. Operators typically require minimal training, often achievable within a few days.
Q4: Are there any raw materials unsuitable for supercritical CO2 extraction?
Materials with high moisture content (>15%), strong polarity, or excessive fiber may pose challenges. Pre-treatment methods like drying, grinding, or co-solvent addition can mitigate these issues.
Q5: What are the key maintenance considerations for these systems?
Regular maintenance includes monthly checks of seals and filters, quarterly cleaning of heat exchangers, and routine inspections of pressure and temperature control systems.
Q6: How can one determine if the extraction process is complete?
Supercritical CO2 extraction is considered complete when:
• The online UV-Vis detector shows no further increase in absorbance.
• The mass balance between input material and extract stabilizes over time.
• The extract yield meets pre-established thresholds based on pilot trials or standards (e.g., GB/T 11538-2022 for essential oils).
• The residue in the extractor shows negligible active content when analyzed by GC-MS or HPLC.
Q7: Can the equipment extract multiple components simultaneously? How is selective separation achieved?
Keywords: multi-stage separation, selective extraction
Answer:
Yes, selective separation can be achieved through a gradient decompression process:
- Primary separation (50→30 bar): Collects large-molecule lipids (e.g., squalene)
- Secondary separation (30→10 bar): Precipitates terpenes (e.g., limonene)
- Tertiary condensation (-20°C): Captures volatile compounds (e.g., rose ether)
- Case study: Lavender extraction yielded 6 distinct components with purity >95%
Q8: What is the required purity of CO2? Does it need to be food-grade certified?
Keywords: CO2 purity standards, food-grade requirement
Answer:
- Industrial grade: Purity ≥99.5% (suitable for non-contact applications like oil recovery)
- Food grade: Purity ≥99.9%, compliant with GB 1886.228-2016
- Pharmaceutical grade: Purity ≥99.99%, microbial limit <100 CFU/g
Recommendation: For cosmetics and food applications, use food-grade CO2 and request an SGS test report for each batch
Q9: What is the operating noise level of the equipment? Does it meet factory standards?
Keywords: equipment noise, environmental compliance
Answer:
Main noise sources and control measures:
- Plunger pump: 85 dB → Reduced to ≤70 dB with soundproof cover
- Compressor: 90 dB →Reduced to 75 dB using magnetic levitation technology
Compliant with GB 12348-2008 industrial noise emission standard (daytime limit: 65 dB)
Q10: How is the waste material handled after supercritical extraction? Is there any residual solvent risk?
Keywords: waste treatment, solvent residue
Answer:
The extraction residue has the following characteristics:
- Safety: CO2 fully evaporates; no solvent residue (detection limit <0.1 ppm)
- Reuse: Plant residues can be converted into feed (protein loss rate <5%)
- Environmental compliance: Certified under ISO 14001 waste management standards
Summary: Why Invest in Supercritical CO2 Extraction?
✅ Environmentally Friendly: Uses non-toxic, non-flammable, recyclable CO2 — aligning with green chemistry principles.
✅ High Selectivity: Tailors pressure and temperature to target specific compounds with minimal degradation.
✅ Low Residue Risk: Leaves no harmful solvents behind, suitable for food, pharma, and cosmetics.
✅ Scalability: From lab-scale R&D systems to industrial multi-ton per day setups.
✅ Return on Investment: Reduced solvent costs, lower energy consumption, and improved product quality ensure long-term profitability.
Get Expert Help in Choosing or Customizing a Supercritical CO2 Extraction System
Choosing the right system can be challenging, especially when balancing capacity, cost, automation, and compliance (FDA, CE, GMP). Whether you’re a startup brand formulating organic essential oils or a pharmaceutical company isolating bioactives, our engineers and consultants can help you:
- Design optimal extraction parameters based on your target compounds.
- Select or customize equipment for your specific raw material and capacity needs.
- Set up pilot production lines to test product yield, purity, and scalability.
- Comply with international standards, including ISO, GMP, CE, and FDA.
Contact us today for a free consultation or a custom quote. [Contact us now]