Selecting a supercritical CO₂ extraction machine requires careful consideration of several factors, including its intended use, technical specifications, equipment quality, safety, brand support, and application scale. Below is a comprehensive guide to making the right choice.
Clarify the purpose of the supercritical CO₂ extraction machine
Supercritical CO₂ extraction technology is widely used across various industries. Identifying the specific application helps in selecting the appropriate pressure, temperature, separation system, and machine capacity.
Common Application Areas
Food and Flavor Industry
- Extracting natural flavors (e.g., vanilla, citrus essential oils)
- Removing caffeine (decaffeinated coffee)
- Extracting plant pigments (e.g., capsanthin, lutein)
Pharmaceuticals and Herbal Medicine
- Extracting active compounds from medicinal plants (e.g., Panax notoginseng saponins, ginsenosides)
- Extracting CBD (cannabidiol) for medical and health products
- Separating bioactive compounds such as flavonoids and polyphenols
Cosmetics and Essential Oils
- Extracting premium essential oils such as rose and lavender oil
- Isolating natural antioxidants like Vitamin E and Coenzyme Q10
Industrial and Environmental Applications
- Removing contaminants and residual solvents from materials
- Extracting nanoparticles and metal-organic frameworks (MOFs)
By understanding the intended use, users can select the right machine with the ideal pressure, temperature range, and separation system for optimal extraction results.
Key technical parameters of supercritical CO₂ extraction machine
Choosing the right technical parameters enhances extraction efficiency and product purity. Here are the essential specifications to consider:
(1) Extraction Pressure Range
Pressure Range | Suitable Compounds | Typical Applications |
Low Pressure (80–150 bar / 8–15 MPa) | Low-polarity, volatile compounds | Essential oils (e.g., lavender, mint), terpenes, caffeine removal |
Medium Pressure (150–300 bar / 15–30 MPa) | Moderately polar compounds | Flavonoids (e.g., ginkgo leaf extract), alkaloids, natural pigments (e.g., capsanthin, chlorophyll) |
High Pressure (300–400 bar / 30–40 MPa and above) | Highly polar or difficult-to-dissolve substances | Lipids (e.g., seabuckthorn seed oil, wheat germ oil), waxes, deep extraction from dense materials (e.g., resins, seeds) |
Key Takeaway: Higher pressure increases extraction efficiency but also raises energy consumption and equipment costs.
(2) Temperature Control Range
- 35–45°C: Suitable for heat-sensitive compounds, such as essential oils, proteins, and polyphenols.
- 45–80°C: Ideal for more temperature-stable compounds, such as some terpenes and flavonoids.
Adjusting the temperature optimizes solubility and enhances the selectivity of extracted compounds.
(3) Extraction Vessel Capacity
Machine Type | Capacity | Best Use Case |
Laboratory-Scale | 0.5–5L | Research and small-scale testing |
Pilot-Scale | 5–50L | Process optimization and small-batch production |
Industrial-Scale | 50–500L+ | Large-scale commercial production |
(4) Separation System
- Single-Stage Separation: Suitable for extracting a single target compound (e.g., essential oils or a specific active ingredient).
- Multi-Stage Separation: Essential for separating complex mixtures and increasing purity, commonly used in pharmaceuticals and food industries.
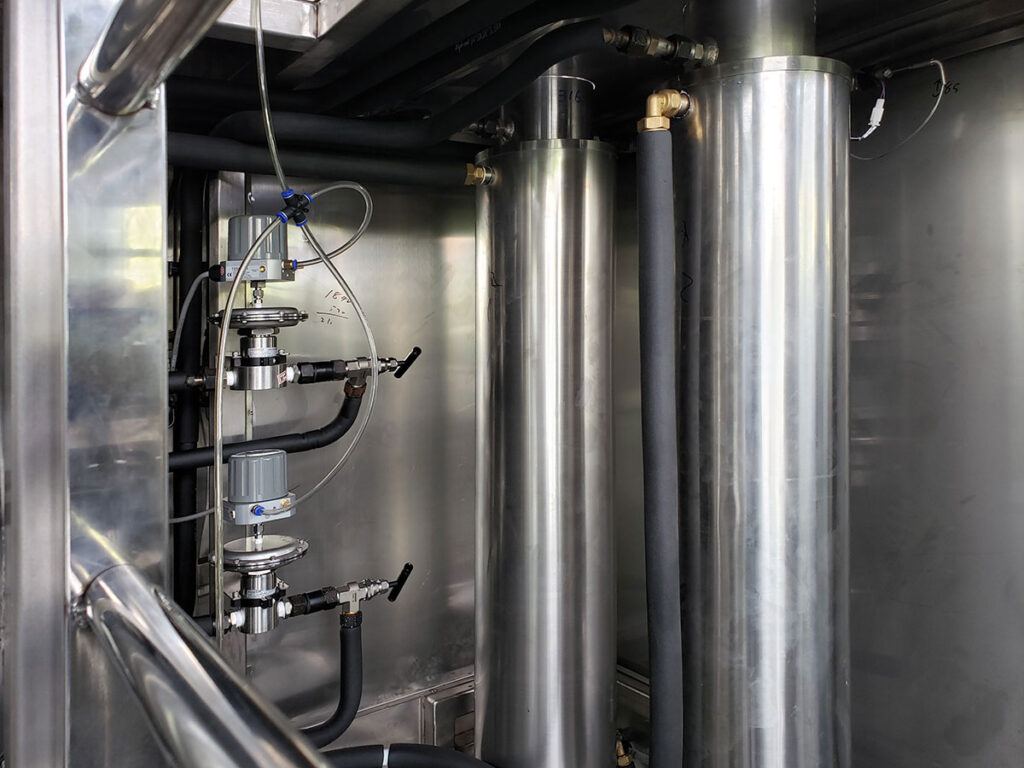
(5) CO₂ Recycling System
- Open System: This system uses CO₂ once and then releases it. It is ideal for small-scale lab setups but incurs higher operational costs.
- Closed-Loop System: Recirculates CO₂, significantly reducing long-term costs, and making it more suitable for industrial production.
Equipment Quality and Safety
Since high-pressure extraction requires robust equipment, it’s crucial to evaluate materials, sealing performance, automation, and cooling systems for long-term reliability and safety.
(1) Manufacturing Materials
- Food-grade stainless Steel (304 or 316L): Corrosion-resistant and meets safety standards for food and pharmaceutical applications.
- High-Pressure Alloy Steel: Used in critical components to withstand extreme pressure and ensure durability.
(2) Sealing Performance
- High-pressure, high-temperature sealing rings such as PTFE (polytetrafluoroethylene) or metal seals prevent gas leakage.
(3) Automation and Control Systems
- PLC (Programmable Logic Controller): Ensures precision and reduces human error.
- Touchscreen Interface: Displays real-time data, including temperature, pressure, and flow rate, for easy monitoring and operation.
(4) Cooling System
- High-Efficiency Heat Exchangers: Prevent overheating and maintain optimal extraction conditions.
Choosing the Right Machine for Your Scale
Before purchasing, consider whether the machine is needed for research, pilot-scale testing, or industrial-scale production.
Application Scale | Machine Capacity | Best Use Case |
Laboratory Research | 0.5–5L | New product development, compound analysis |
Pilot Production | 5–50L | Process optimization, small-batch manufacturing |
Industrial Production | 50–500L+ | Full-scale commercial manufacturing, continuous operation |
Industrial machines typically feature continuous operation and automated control systems to maximize efficiency.
Cost and Energy Efficiency Considerations
Understanding the total cost of ownership is essential. The initial investment, operating expenses, and production efficiency all influence the machine’s long-term value.
(1) Initial Investment
- Prices range from tens of thousands to several million depending on capacity, features, and brand.
(2) Operating Costs
- Includes CO₂ consumption, electricity, and maintenance.
- Closed-loop CO₂ systems reduce long-term costs by recycling CO₂ instead of venting it after each use.
(3) Production Efficiency
Machines with a higher degree of automation may have a higher upfront cost but significantly reduce labor expenses and increase processing speed.