In today’s era of natural product innovation and sustainable manufacturing, supercritical CO2 extraction (SFE) has emerged as the preferred method for extracting high-value plant oils and natural aromatics. Compared to traditional methods like solvent extraction or steam distillation, SFE offers low-temperature operation, zero solvent residues, and high selectivity. As a result, it has gained popularity among essential oil producers, functional food manufacturers, and natural skincare brands worldwide.
This in-depth article explores how SFE works for plant oil and aromatic extraction, its mechanisms, equipment setup, key botanical sources, commercial applications, and future trends. Whether for research or commercial use, this guide will help you master this pivotal technology.
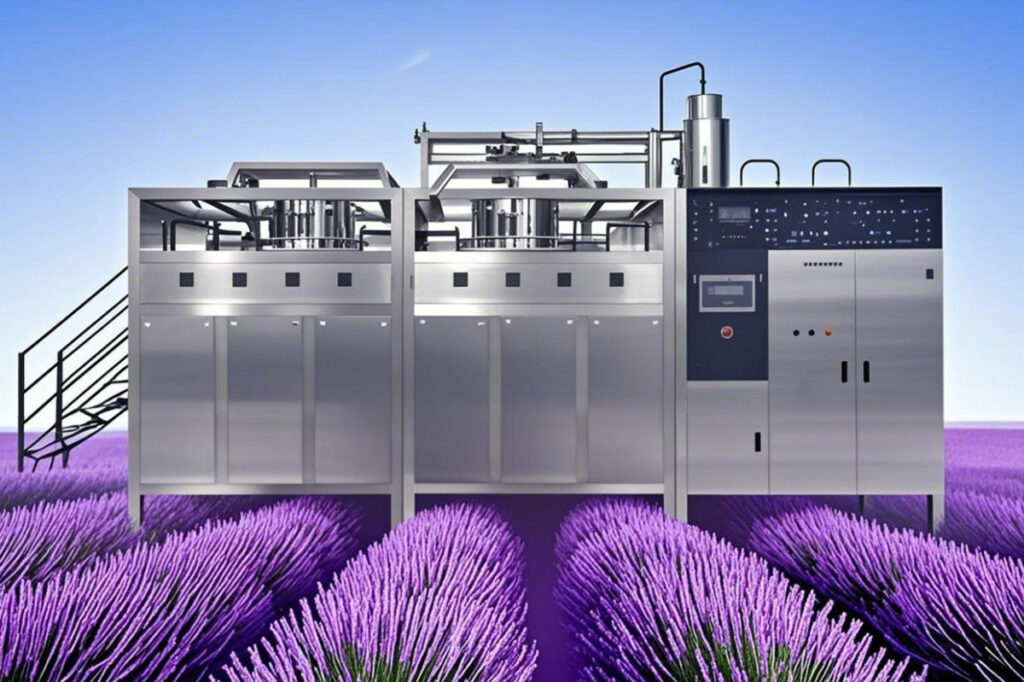
What is Supercritical CO2 Extraction?
Supercritical CO2 refers to CO2 that exists in a hybrid state between gas and liquid, achieved at temperatures above 31.1°C and pressures over 7.38 MPa. In this state, CO2 behaves like a gas in terms of diffusion and like a liquid in terms of solvating power, making it an ideal solvent for lipophilic and mildly polar compounds.
Key Characteristics of Supercritical CO2
- High diffusivity → Penetrates plant matrices efficiently
- Tunable density → Adjustable solvation capacity
- Inert and non-reactive → Prevents oxidation and degradation
These features make CO2 perfect for extracting:
- Volatile oils (e.g., terpenes, alcohols)
- Fat-soluble vitamins (e.g., Vitamin E)
- Lipophilic polyphenols
- Tocopherols, sterols, and carotenoids
Why Choose CO2 Extraction for Plant Oils and Aromatics?
Traditional techniques such as steam distillation and solvent extraction present challenges: thermal degradation, solvent residues, and limited selectivity. In contrast, supercritical CO2 extraction offers a cleaner, gentler, and more controllable process:
Process | Supercritical CO2 | Steam Distillation | Solvent Extraction |
Operating Temperature | 30–50°C | >100°C | 50–70°C |
Active Compound Retention | Excellent | Often Degraded | Moderate |
Solvent Residue | None | None | Potentially Toxic |
Selectivity | High & Adjustable | Low | General |
Scalability | Industrial-Friendly | Low Cost, Low Yield | Risky at Scale |
✅ For heat-sensitive botanicals rich in aromatic or complex molecules, CO2 extraction is the superior method.
Recommended Botanicals & Key Bioactive Compounds
Below are some high-demand botanicals along with their main active constituents and applications:
1. Rose (Rosa damascena)
- Bioactives: Geraniol, Phenylethanol, Nerol, Linalool
- Features: Aroma-rich and heat-sensitive
- Applications: Luxury perfumery, anti-allergic skincare, aromatherapy
2. Sea Buckthorn (Hippophae rhamnoides)
- Bioactives: Linoleic acid, Alpha-linolenic acid, Sterols, Vitamin E
- Features: Omega-rich, highly antioxidant
- Applications: Nutraceuticals, anti-aging skincare oils
3. Frankincense (Boswellia serrata)
- Bioactives: β-Boswellic acid, α-Boswellic acid, Terpenoids
- Features: Anti-inflammatory and traditional medicinal value
- Applications: Aromatherapy, skin repair products
4. Peppermint (Mentha piperita)
- Bioactives: Menthol, Menthone, 1,8-Cineole
- Features: Cooling sensation, refreshing scent
- Applications: Oral care, aromatics, essential oils
5. Grape Seed (Vitis vinifera)
- Bioactives: Linoleic acid, Proanthocyanidins, Vitamin E
- Features: Lightweight oil with high antioxidant potential
- Applications: Skin oils, hair serums, dietary supplements
Equipment Configuration and Process Flow
Key Components of an SFE System:
- Raw Material Preprocessing Unit: Drying and milling to <0.5 mm
- Extraction Vessel(s): 1–5 tanks rated to 30 MPa
- Multi-stage Separator(s): Control pressure for selective deposition of oils/aromatics
- CO₂ Storage & Compression: Recirculates CO2 to reduce cost
- Thermal Control System: Ensures product bioactivity during processing
General Workflow:
Raw Material → Pressurization & Heating → Extraction → Decompression & Separation → CO2 Recovery → Collection of Essential Oil or Lipid
Applications and Industry Use Cases
1. Natural Skincare
- Purpose: Carrier oils, bioactives, luxury fragrance oils
- Case: Rose CO2 extract featured in premium serum with claim “100% solvent-free natural purity”
2. Aromatherapy Products
- Purpose: Massage oils, diffusers, and mood relaxation
- Case: U.S. wellness brand uses peppermint CO2 extract for meditation-friendly aroma profiles
3. Functional Foods & Supplements
- Purpose: High-purity oil capsules, antioxidant beverages
- Case: German nutraceutical brand markets sea buckthorn CO2 extract as “no chemical treatment, 100% CO2 extracted”
FAQ(supercritical CO2 extraction, essential oil extraction, plant lipid CO2 extraction)
H3: Can supercritical CO2 extraction improve oil purity?
Yes. Its selectivity and precise control enable the extraction of high-purity compounds such as lipids, sterols, and carotenoids, especially with dual-separator systems.
H3: Is the technology expensive?
The initial equipment investment is relatively high, but long-term costs are low thanks to CO2 recyclability. Products such as high-grade essential oils yield high returns.
H3: Can it extract water-soluble compounds?
Not directly, since CO2 is non-polar. However, using polar co-solvents like ethanol can broaden the compound spectrum for co-extraction.
Conclusion: A Sustainable and High-Value Path Forward
Supercritical CO2 extraction is not merely a processing technique—it’s a strategic green innovation. It enables product premiumization, sustainability, and differentiation while bridging the gap between research and commercial production.
As demand grows for essential oils, plant lipids, and functional actives, SFE is shifting from “lab-scale tech” to “high-end manufacturing”. Now is the time for formulators and manufacturers to leverage their advantages and innovate naturally.